s.quality | Intelligent quality monitoring & AI-supported process control in real time
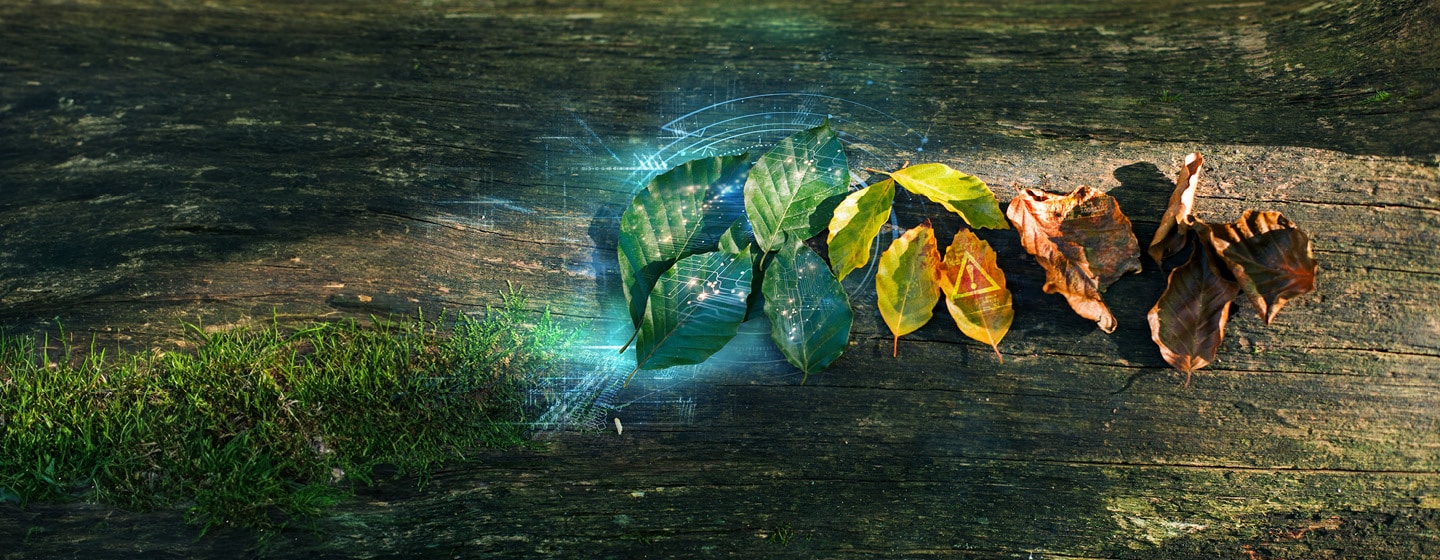
Do you want to lower your costs by avoiding expensive re-production? Do you want to receive updates on production quality, ideally during ongoing production? Do you want to be informed about deviations from the standard process in time to be able to take measures as quickly as possible?
Then you need an intelligent monitoring solution which can do all of this. You need s.quality!
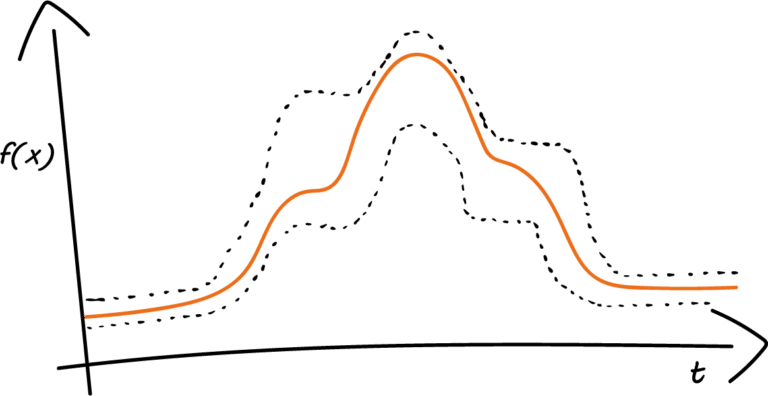
Evaluates the product quality and the system condition during the running process.
The increasing product and process requirements set high standards for production quality and therefore also for the entire production process. It is therefore important to make production processes transparent so that process deviations can be recognised and rectified as quickly as possible with the help of artificial intelligence.
Our software solution: s.quality
Even the smallest deviations of individual process parameters can have a massive impact on product quality. Recalled products and large quantities of rejects are often the result — a costly and time-consuming affair for any company. Our innovative software s.quality processes your data already during ongoing production and evaluates it using artificial intelligence. The digital solution helps you monitor the measured values and process parameters of your plant to ensure that your end product meets the required quality standards. s.quality permanently monitors your recurring processes and measurement operations, detecting any faults or deviations from the standard process at an early stage. An extremely high data resolution of up to 1 MHz can be processed. With our software solution, our customers are optimally equipped for quality assurance and monitoring in all process and production stages. By using s.quality, you can boost your production performance while reducing the failure rate in order to assure highest production quality. Our software solution helps you complete your tasks even more efficiently and precisely, and identify and correct faults in time.
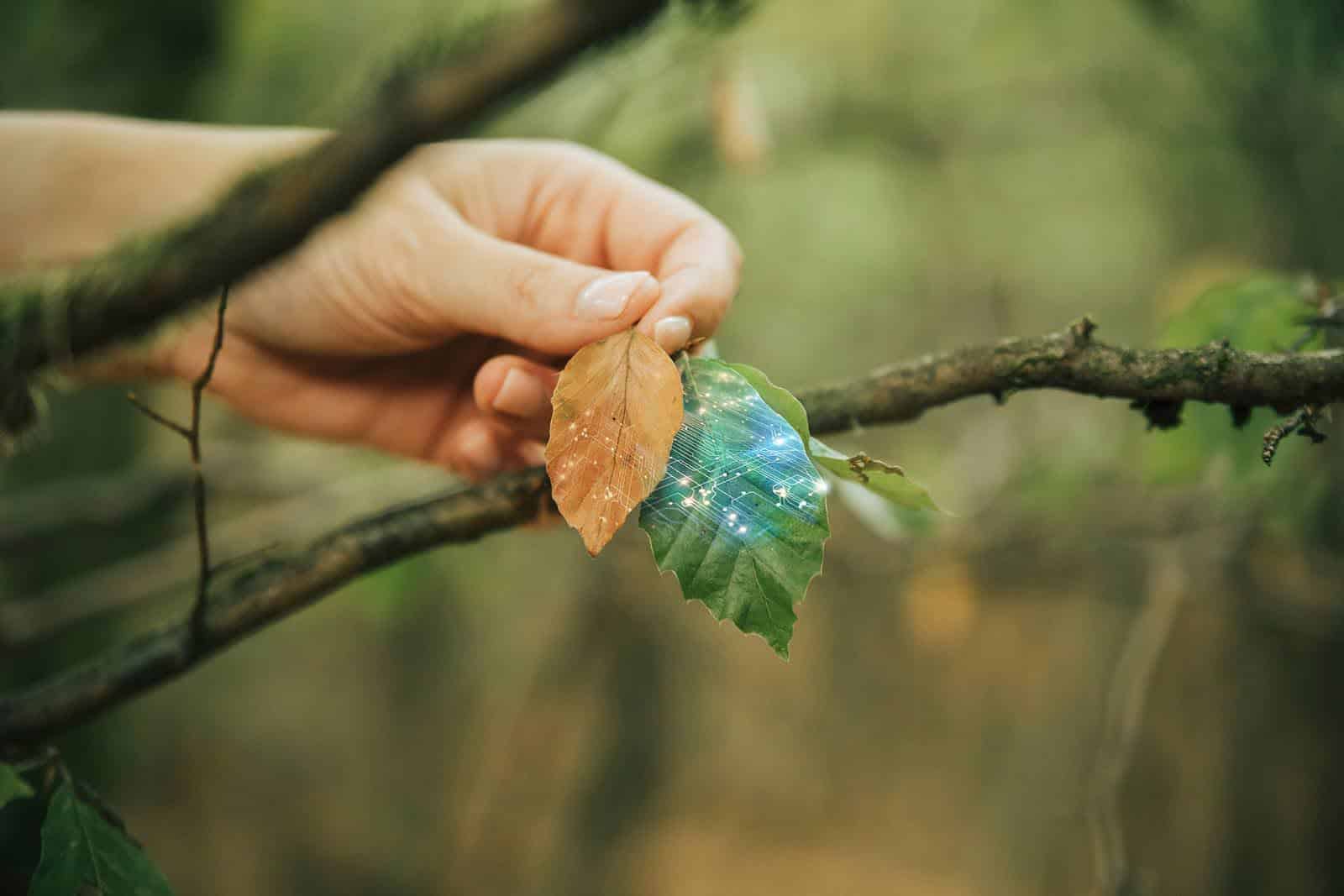
The algorithm library of s.quality
s.quality uses artificial intelligence (AI) to identify deviations in the production process. A model is trained with historical data to detect any abnormal behaviour in new data sets. Self-learning statistical methods are used to identify a standard structure for each test channel. If the profile of a measured value deviates significantly from the dynamic tolerance threshold defined by the user, the anomalies are documented as errors and analysed. Only very few settings are required to obtain a clear and instant overview of all measured values and any faulty products, components or processes. Machine learning makes it possible to adapt this procedure to defined standard processes. s.quality can also be integrated into the manufacturing process and automatically communicate the condition of the inspected product or monitored process to the machine control.
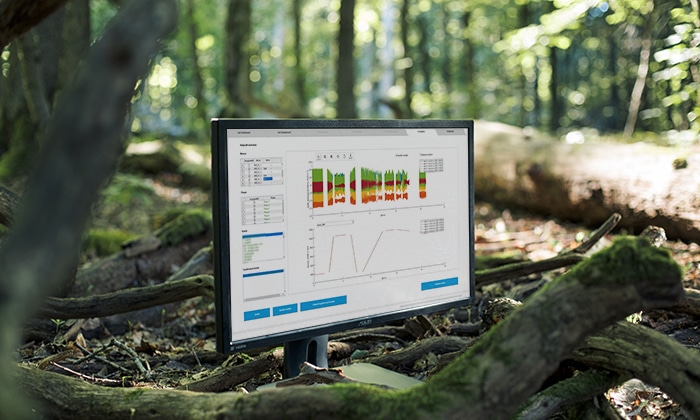
The benefits of s.quality
- permanente Hintergrundüberwachung kritischer PrContinuous background monitoring of critical process variables
- Classification of anomalies through self-learning monitoring algorithms
- Root cause analysis of changes in production quality
- Can be used in all process and production stages
- Unsupervised and supervised learning
- Dynamic threshold for continuous process and product quality assessment
- Process evaluation possible during live operation or offline
s.quality in a nutshell
Data:
- High-resolution process values of individual production steps
- Discrete production monitoring (product ID)
- No pre-classification of product quality necessary
Our solution for assessing manufacturing quality during production:
- Identification of deviations in product quality
- Fully automated classification of quality levels (OK / not OK)
- Understanding individual differences in quality
Result:
- Stand-alone / On-premise solution
- Full solution · live assessment and reporting
Haben Sie Fragen zu unseren Produkten? Dann vereinbaren Sie einen Termin mit uns. Unser Team wird Sie gerne in einem persönlichen Gespräch oder per E‑Mail beraten.
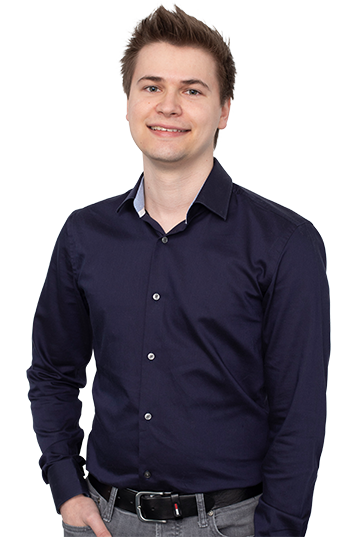
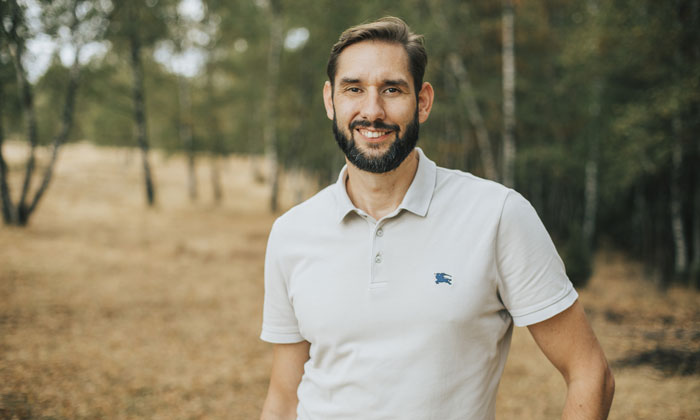
ifm statmath gmbh Managing Director